Peek Is a Great Material for Injection Molding
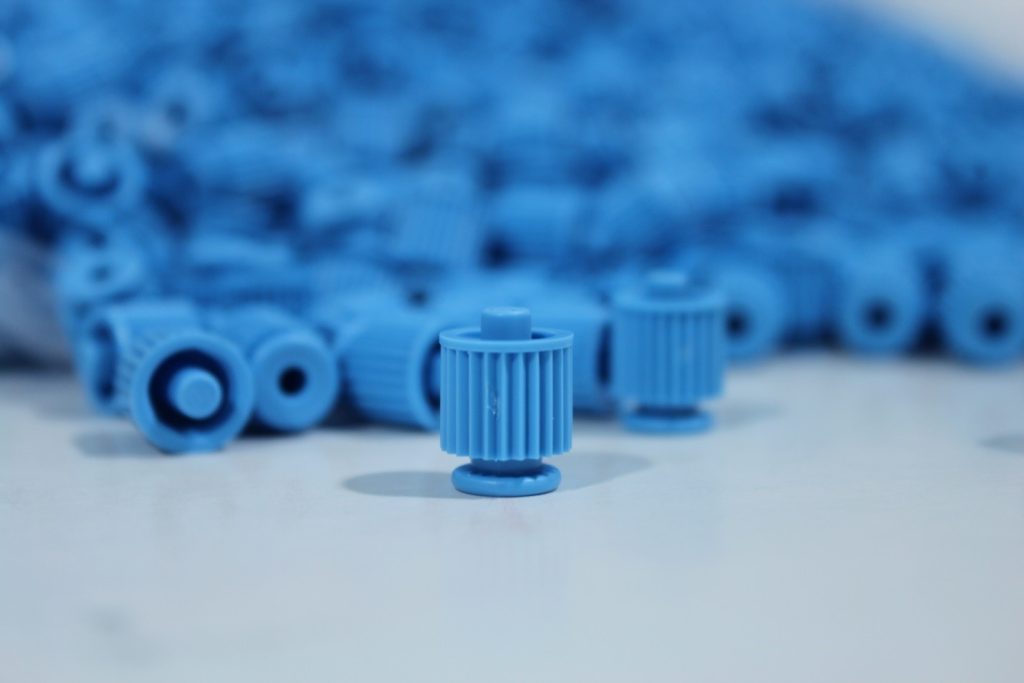
Peek is a great material for injection molding. It can survive multiple sterilization cycles without sacrificing its mechanical strength and resistance to gamma and EtO radiation.
However, injection molding peek isn’t a walk in the park. This unique polymer presents special challenges that most injection machines are not prepared to handle.
Optimal Injection Pressure
Injection molding requires a power greater than or equal to the resistance that molten material creates in the process of flowing into the mold cavity. The injection machine provides this power by increasing the internal pressure in the machine during the injection action.
PEEK is also sterilizable using radiation, making it useful for production of sterilization-critical medical equipment such as reusable surgical tools and catheters. However, the high temperatures and pressures required by this process can cause a number of injection molding defects, including cold spots, silver streaks, pores, weld lines, and warpage.
Changing the injection pressure can reduce these defects, but it is important to consider all of the variables that affect injection pressure. This includes nozzle contact pressure and line pressure. It is important to ensure that these pressures are not higher than injection pressure to avoid damage to the nozzle and runner system. Also, if the machine is used to produce other types of plastics, all traces of those materials should be removed from the equipment before running PEEK.
Optimal Injection Temperature
PEEK is a high-performance plastic, but it’s not a walk in the park to mold. It has a very high melting point, which means it needs to be processed in machines that are specially equipped for working with this type of polymer. If not, you risk damaging the equipment and creating quality problems with your products.
When you’re processing PEEK, you also have to keep the machine temperature at a certain level. If it goes too high, the non-PEEK parts in the injection molding machine can degrade and create dark specks on the finished product. These specks will ruin the appearance and quality of the parts and can lead to part rejection.
To avoid this, you need to clean your equipment before starting a production run with PEEK. This includes cleaning the screw and barrel of the injection molding machine, as well as the nozzle and runner system. If possible, dedicate the injection molding machine to PEEK only, so that you don’t have to worry about contamination from other lower-melting plastics.
Optimal Holding Pressure
PEEK polyetheretherketone is an engineering plastic with excellent mechanical properties, and it has a wide range of uses. However, if it is not properly handled during injection molding, the resulting product can suffer from a variety of defects such as cold material points, silver streaks, porosity, fusion marks, and warpage.
To reduce the risk of these defects, it is important to minimize the initial transfer pressure and the holding pressure of the machine. In addition, it is advisable to profile the injection speed by increasing it initially so that the runner system and the part cavity are filled quickly, and then to decrease the speed in order to prevent surface flow defects.
It is also important to clean the entire injection molding machine before starting a run with PEEK. This includes the screw and barrel, nozzle, runner system, and any containers that hold the regrind. Also, all the auxiliary equipment like drying ovens should be cleaned before running with PEEK. This is because other materials degrade at PEEK’s processing temperatures and can cause dark specks on the finished part.
Optimal Mold Temperature
Peek is a special thermoplastic with unique mechanical properties. It is used in high-performance applications and is very resistant to corrosion, oxidation, and thermal fatigue. PEEK’s exceptional properties are a result of its semi-crystalline molecular structure, which allows it to maintain both strength and flexibility.
Injection molding requires a precise processing temperature to ensure proper crystallization of the polymer and avoid warping. If this temperature is not maintained, the molded part will have a rough surface and may even crack. It is also important to minimize shrinkage, as this can cause the injection molded product to deviate from its original shape and cause warping of the mold cavity.
The tensile test results from nine groups of orthogonal experiments show that the injection temperature and injection pressure have the greatest influence on the molded PEEK products’ strength, while the injection speed has little effect. The injection time should be 6 s to ensure that the whole cavity is filled with enough molten material. The holding time should be 8 s to replenish the volume reduction caused by the decrease of the melt temperature in the cavity and to prevent the generation of air holes after the removal of the sprue condensate.peek injection